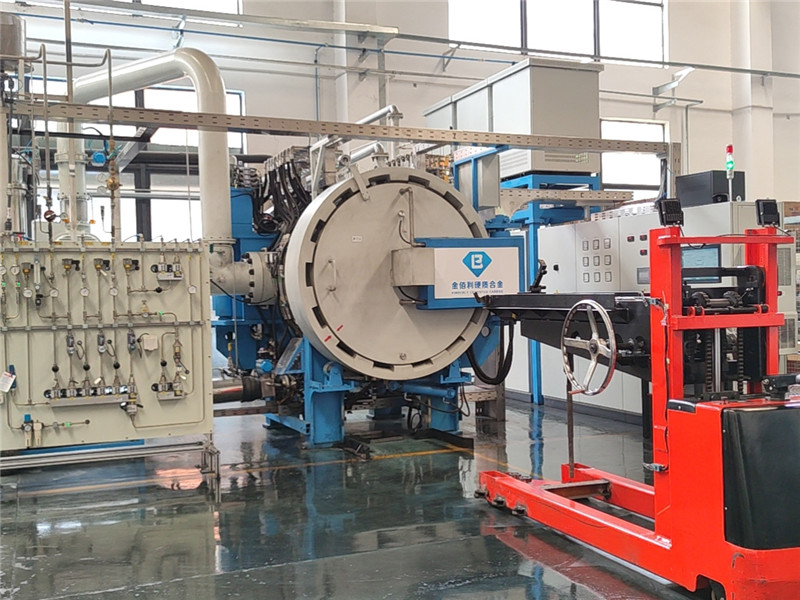
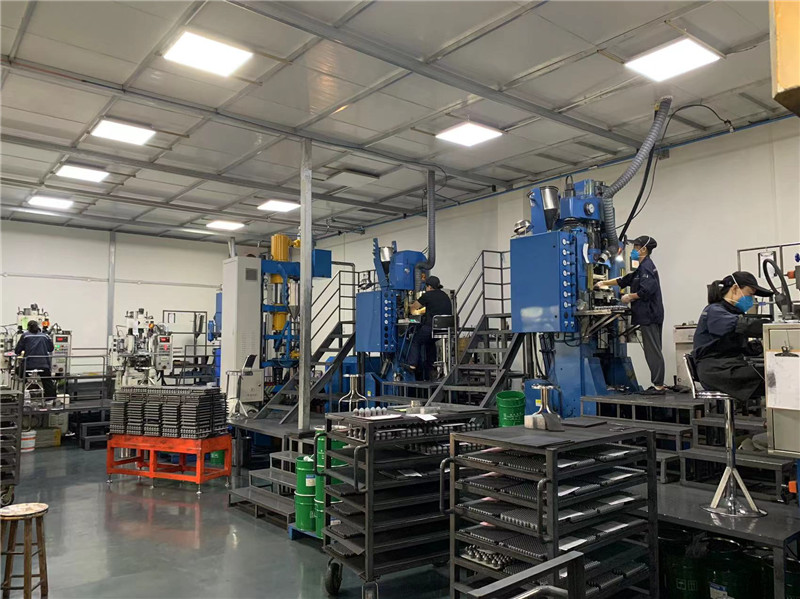
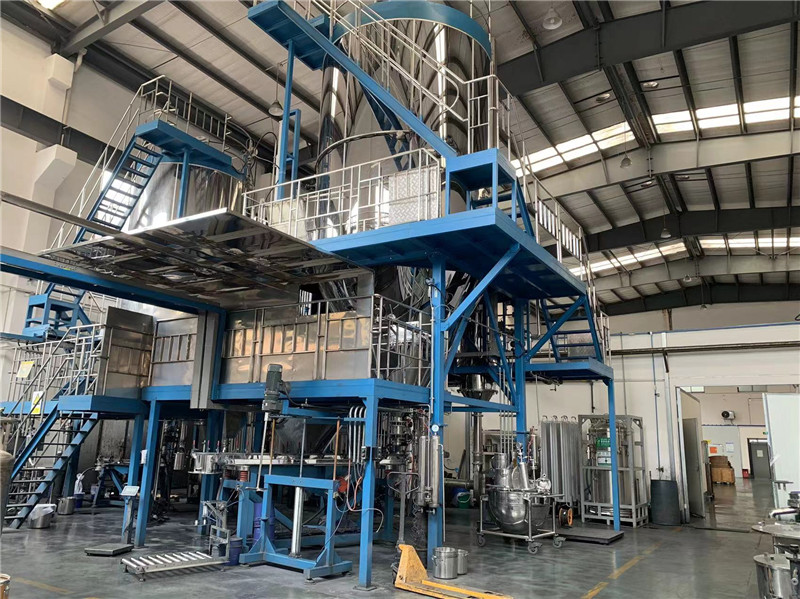
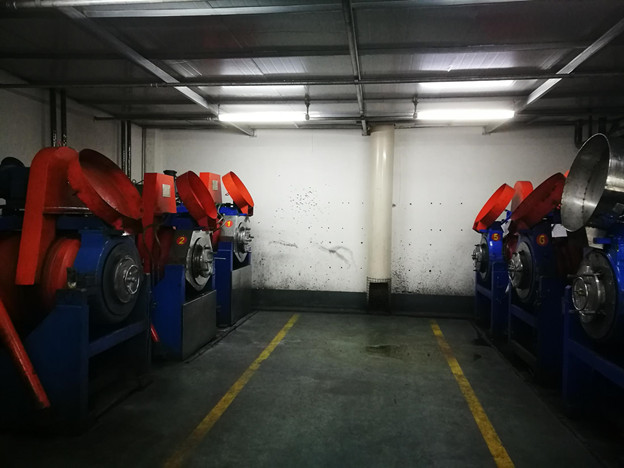
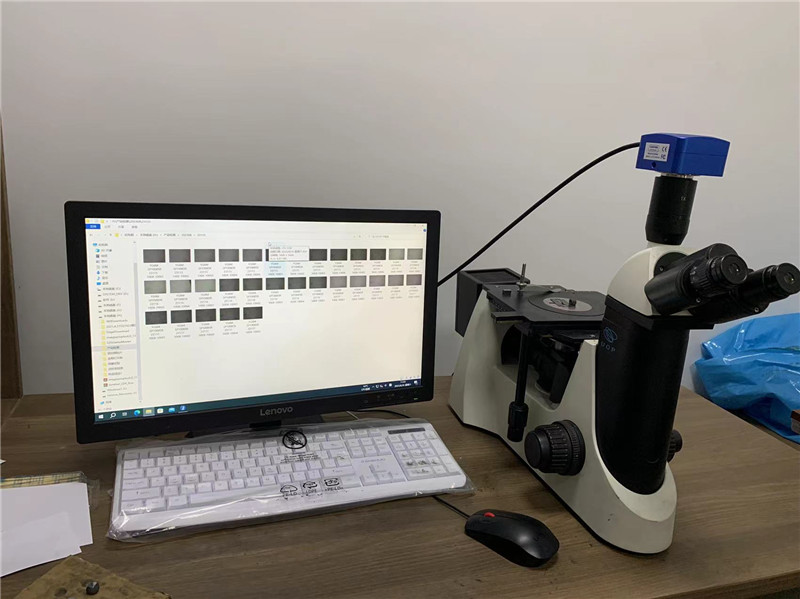
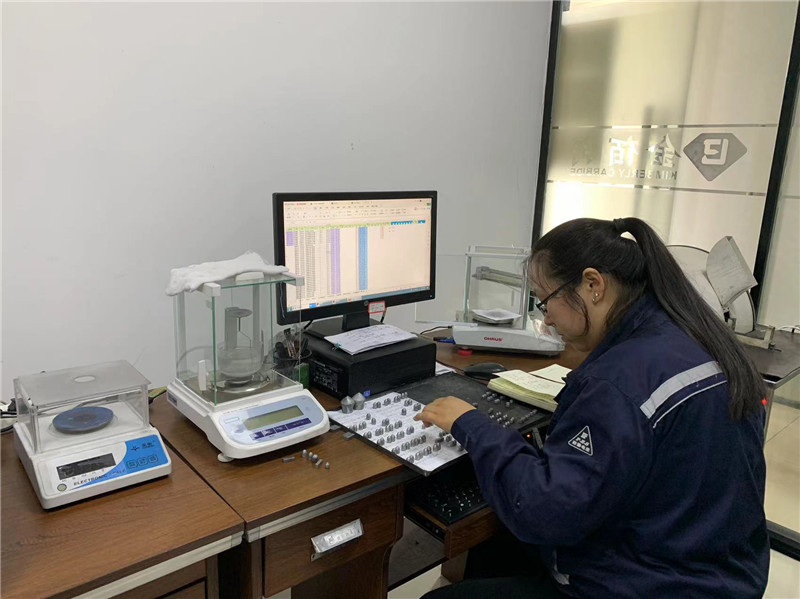
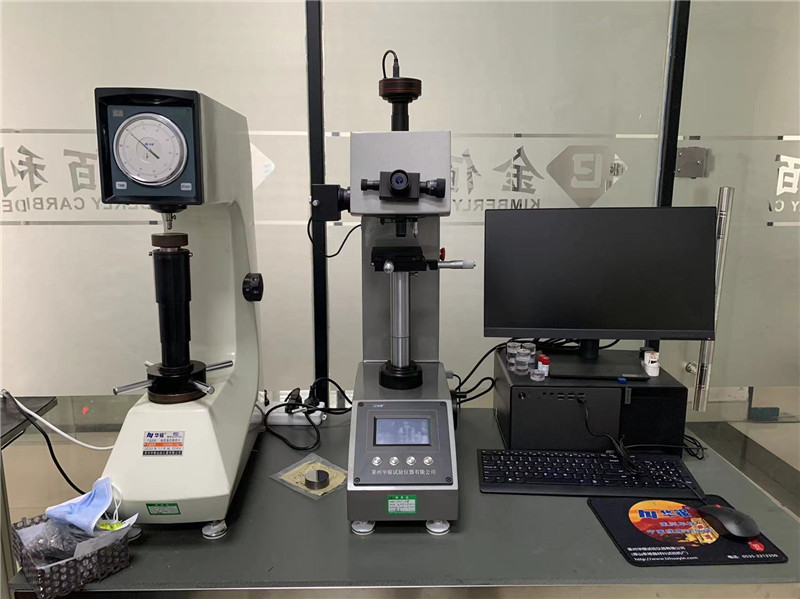
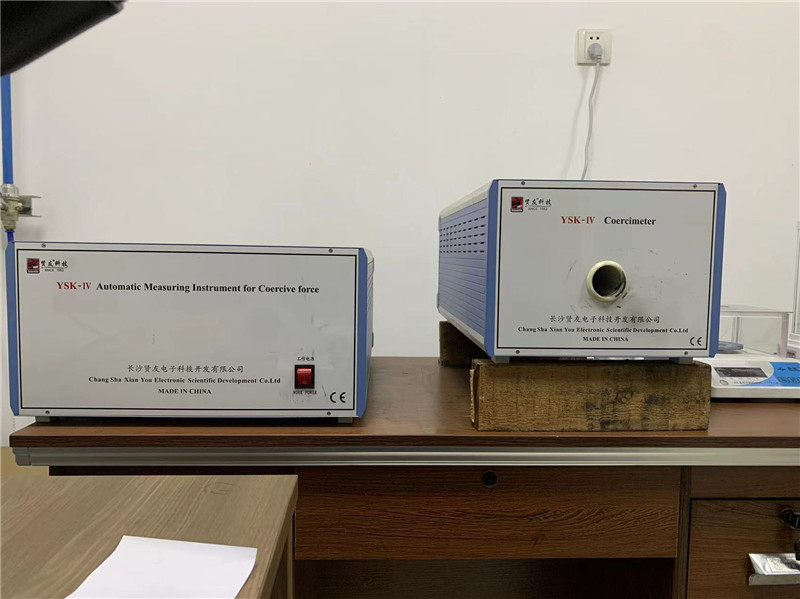
Equipment
We utilize imported materials and domestically renowned "Three High" primary tungsten carbide from reputable manufacturers as raw materials.
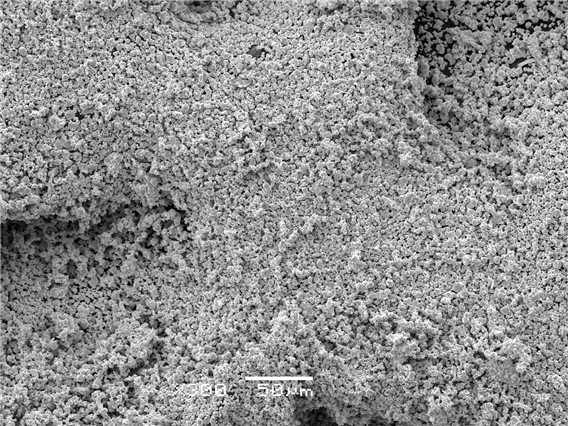
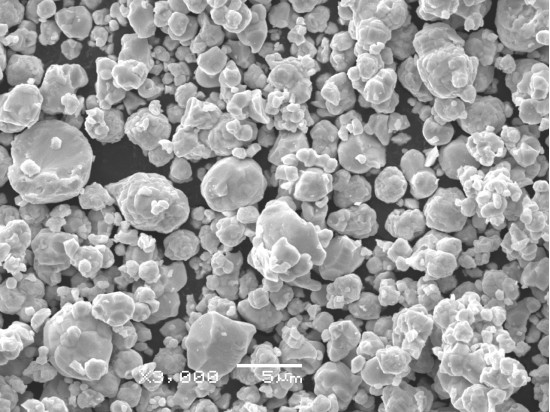
Premium Materials
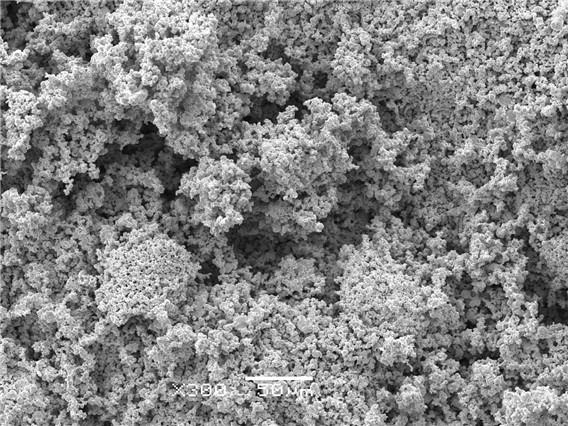
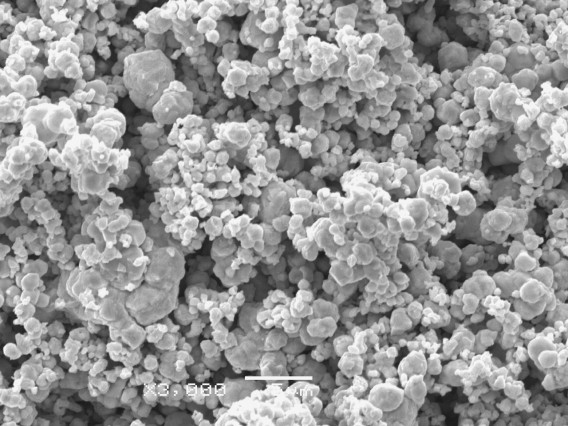
Conventional Substances
We adopt the international advanced precision cemented carbide production process to manufacture high-quality alloy products.
Our blended ball milling preparation workshop has been upgraded to achieve intelligent and automated control. Through an automated control system, we manage parameters such as rotational speed, time, temperature, etc. Any anomalies are promptly alerted, and comprehensive data analysis is conducted to continually optimize the process control parameters.
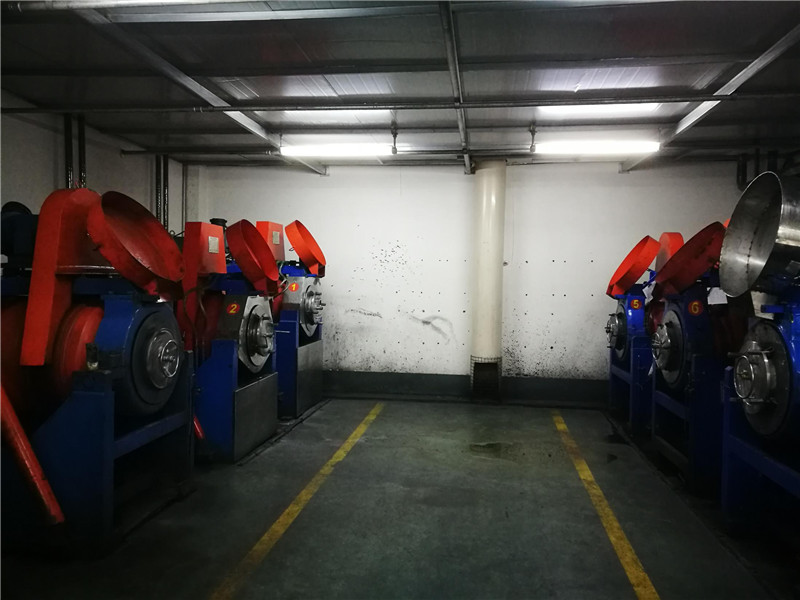
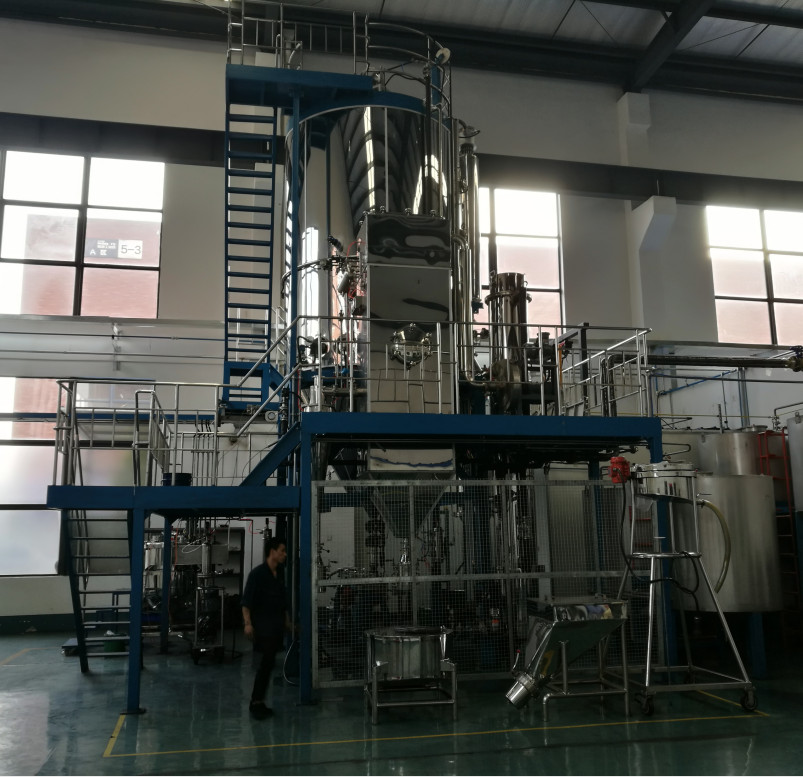
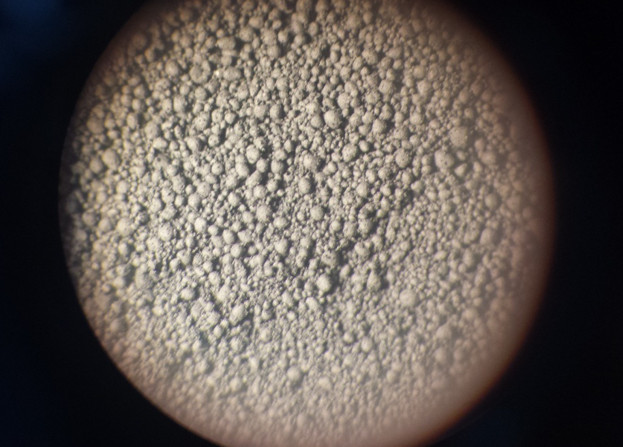
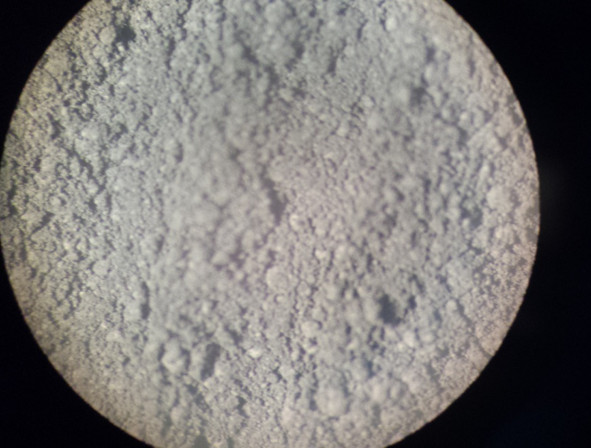
We utilize internatio-nally advanced spray drying granulation tech-nology, which compar-ed to traditional manual granulation, effectively isolates air and dust, resulting in uniformly sized powder particles and consistent quality.
Compaction and Molding Workshop:
In our compaction process, we employ advanced machinery including a 60-ton TPA automatic press and a 100-ton automatic hydraulic press. This results in uniformly distributed raw product density and high precision in product dimensions. The workshop maintains positive pressure ventilation, year-round temperature and humidity control, as well as air purification measures to ensure a contamination-free production environment and product quality throughout the manufacturing process.
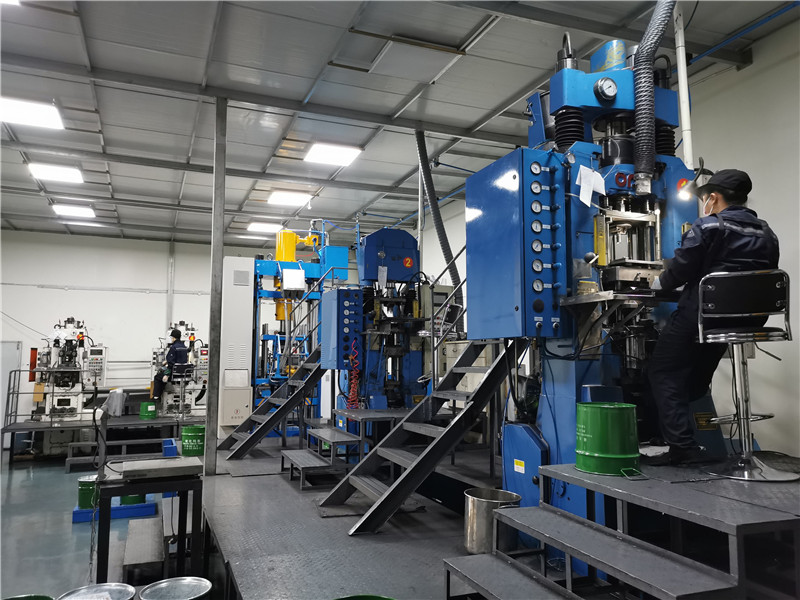
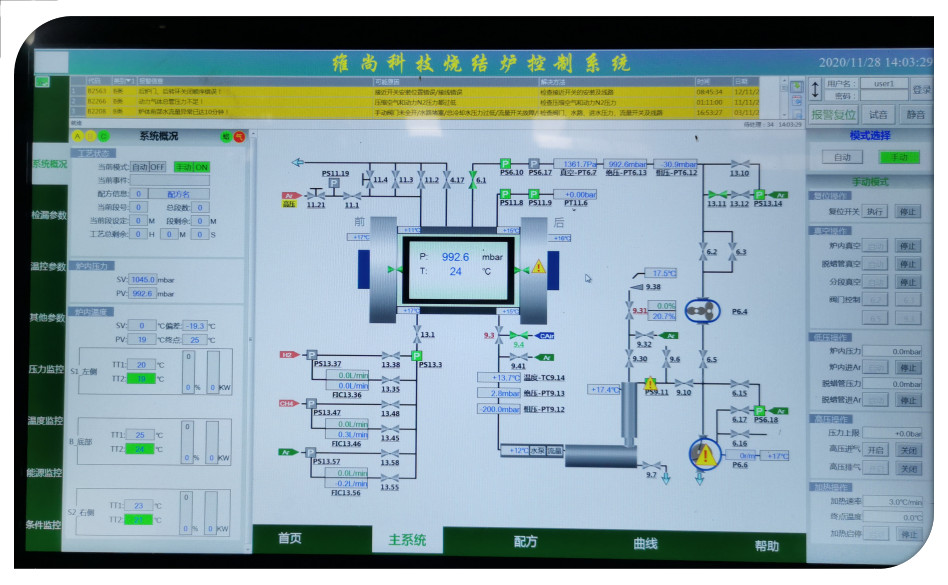
In the past 50 years, cemented carbide sintering technology has undergone a progressive evolution from hydrogen furnaces to vacuum furnaces, and finally to pressure furnaces. Pressure-assisted sintering has emerged as the forefront alloy sintering technique globally. This approach combines debinding, vacuum sintering, and pressure sintering into a single step, reducing product porosity and achieving a level of alloy density akin to fully dense materials.
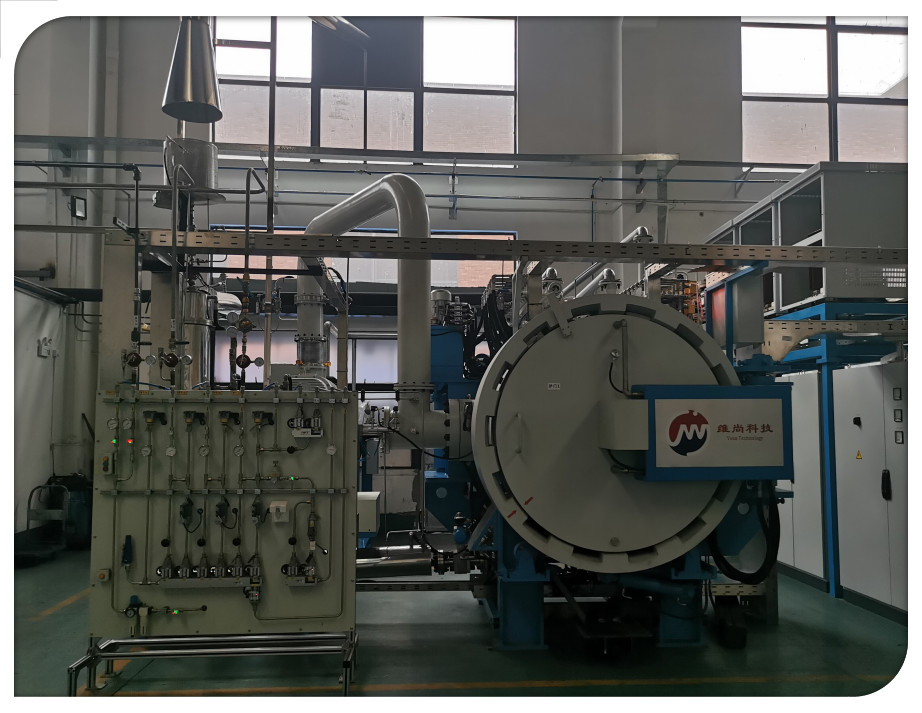
Nine-Step Quality Control Process in Alloy Production:
1. Testing of Raw Material's Chemical and Physical Properties
2. Experimental Performance Testing of Raw Material Ball Milling
3. Sampling and Testing of Physical Properties of Mixed Ball-Milled Materials
4. Identification through Sampling and Testing of Physical Properties of Mixed Spray-Milled Materials
5. Initial Performance Testing of Compaction Calibration and Molding
6. Self-Inspection of Production Quality during Compaction
7. Reinspection of Quality by Compaction Quality Personnel
8. Testing of Physical and Mechanical Properties of Sintered Finished Products
9. Inspection of Finished Product Models, Dimensions, Appearance, and Defects.
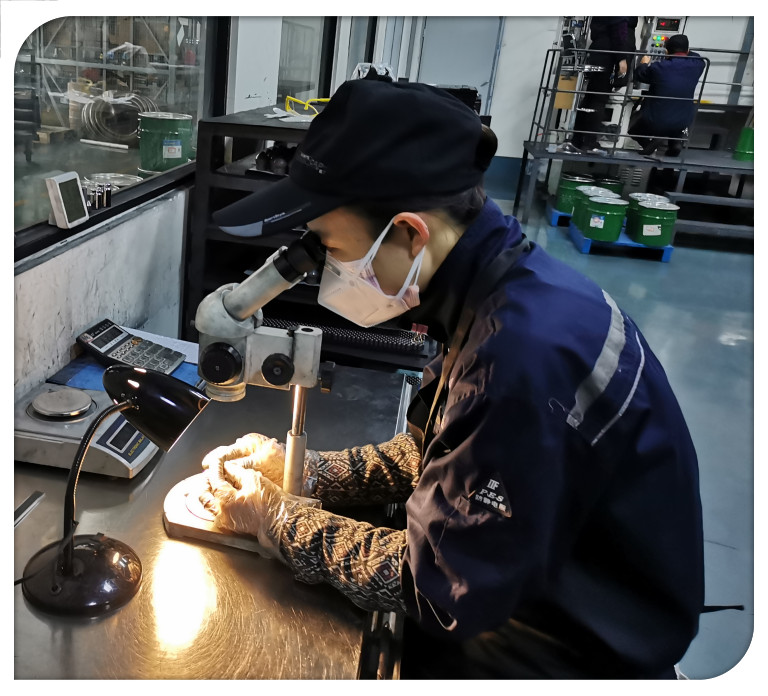